Power Quality and Generators - Part 9: Design Criteria for Grounding
Editor's Note
This is the ninth installment in an ongoing series that will cover basic engineering and code issues for standby generators. In a subsequent column, the author will address the National Electrical Code (NEC).
Standby generator system grounding must be understood to ensure proper operation of the critical electrical systems. It is not my intent to cover all of the issues involved in proper grounding of emergency standby systems, but to clarify some of the main issues that tend to come up in most projects.
A standby generator system uses either a three- or four-pole automatic transfer switch (ATS) to transition from utility electrical power to standby electrical power in the event of a loss of normal electrical service, as shown in Diagrams 1 and 2 below.
Three-pole vs. four-pole ATS
In a typical three-phase electrical distribution system, the engineer or system designer has the choice between a three-pole or four-pole ATS. There are certain circumstances where a four-pole ATS will be required, typically where the electrical distribution system has two or more levels of ground fault sensing and two or more ATS.
Per the National Electric Code, Article 230-95, ground fault protection is required on solidly grounded equipment 277/480-volt rated at 1,000 amps or more. Where a single level of ground fault is required by NEC, Section 517, hospitals will require a second level of ground fault protection to ensure service continuity during a ground fault on a branch feeder.
Although not required by code, other critical facilities may opt for multiple levels of ground fault protection to minimize the effect of a short to ground. In these cases of multiple levels of ground fault and of multiple automatic transfer switches, a four-pole ATS is required. If the neutral is not switched, neutral current due to unbalanced loading or non-linear loads can split in the parallel paths and cause nuisance tripping of the ground fault sensor. A four-pole ATS switches the neutral; a three-pole does not.
If the generator main breaker is rated at 1,000 amps or more, and is at 480-volt three-phase, per the NEC 700-7, ground fault indication is required. A ground fault will set off an alarm and will not trip the generator breaker. The alarm contacts should latch so that if the fault occurred between the generator and the ATS, the alarm would still register a fault when the system returned to normal power. The location of the alarm strobe and potential remote alarm must be coordinated with the design team and the owner. A four-pole ATS is required in this situation for proper operation of the ground fault sensor. The generator system ground must be located at the generator side of the ground fault sensor so that ground faults can be detected.
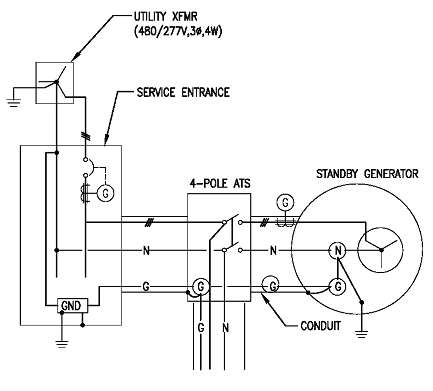
When the generator is considered a separately derived source, the neutral and ground are tied together at the generator and a four-pole ATS must be used. The neutral is switched at the ATS.
If the generator ground is connected to the neutral at the main service ground bar and the generator neutral and the service neutral are solidly connected through the ATS, the generator is not considered a separately derived system and would use a three-pole ATS as shown in Figure 2. Per NEC 2002, Section 250-20, a generator system that utilizes a three-pole ATS is not considered a separately derived source. Three-pole ATS are generally less expensive and take up less space than four-pole ATS.
NEC Section 250-20 (5) FPN 1 indicates that an alternating-current power source such as an on-site generator is not a separately derived system if the neutral is solidly interconnected to a service supplied neutral.
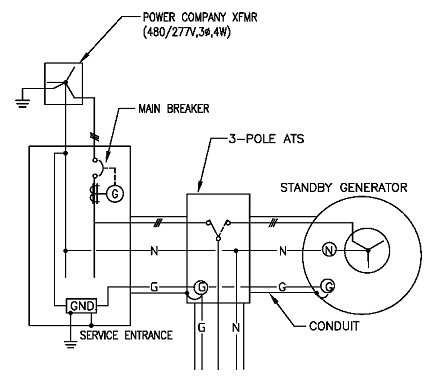
When the generator is not considered a separately derived source, the neutral and ground are not tied together at the generator and a three-pole ATS must be utilized. The neutral is solidly connected at the ATS to allow the generator neutral to be connected to the main service ground at all times (when the load is being served from either the main service through the serving electrical utility or from the standby generator).
Because a generator that feeds a three-pole ATS is not considered a separately derived source, only the frame of the generator is grounded at the generator and not the neutral. On the other hand, a generator feeding a four-pole ATS is considered a separately derived source and the neutral is grounded at the generator.
In addition, a four-pole ATS is better than a three-pole switch from a maintenance perspective. With the latter, if the main service is taken offline for maintenance and the standby generator is running to serve the critical and life safety loads, the standby generator is still relying on the main service ground connection to the neutral for the return path of any ground fault.
If maintenance personnel are not aware of this grounding configuration, and maintenance is performed on the main service ground when the service is offline and the standby generator is running, the standby generator would no longer be properly grounding. This could be a serious safety concern and could potentially allow fault currents to flow without tripping the over current protective device.
Grounding electrode system requirements
NEC 2002, Section 250.50, defines the requirements for the grounding electrode system for the main electrical service. This section indicates that, "If available on the premises at each building or structure served, each item in 250.52 (A) (1) though (A) (6) shall be bonded together to form the grounding electrode system."(A) (1) through (A) (6) are noted below and include the following:
- Metal underground water pipe
- Metal frame of a building or structure
- Concrete encased electrode
- Ground ring
- Rode and pipe electrode
- Plate electrodes
This section of the NEC further states, "Where none of these electrodes are available, one or more of the electrodes specified in 250.52 (A) (4) through (A) (7) shall be installed and used." (A) (4) through (A) (7) are noted below and include the following:
- Ground ring
- Rode and pipe electrode
- Plate electrodes
- Other local metal underground system or structures
The NEC 250.52 (A1) also states, "If the water pipe is the only source used it must be connected within 5' of entering the building."
Most generator systems are solidly grounded (direct connection with no intentional impedance), but intentional impedance can be added to the grounding system to allow a phase-to-ground fault to occur without taking down the standby system.
A high resistance ground system allows a fault to ground to occur without requiring the overcurrent protective device to trip. In these systems, the added resistance usually will only allow about 10 amps of fault current to flow through the system. The amount of intentional resistance should be carefully evaluated, as the total fault current should be at least equal to the charge current of the system.
NEC Section 250.36 states that high-impedance grounding systems in which a ground impedance, unusually a resistor, limits the ground fault current to a low value shall be permitted for three-phase AC systems of 480 volt to 1,000 volts, where the following conditions are met:
- The conditions of maintenance and supervision ensure that only qualified persons service the installation
- Continuity of power is required
- Ground detectors are installed on the system
- Lines to neutral loads are not served
Grounding methods
Fault currents occurring in high impedance grounded systems should be investigated immediately. If left to continue, a phase-to-ground fault could potential grow into a phase-to-phase fault. High-impedance grounded systems will not reduce the current from a phase-to-phase fault, the overcurrent protective device will trip and critical loads can go down.
Another method of grounding for standby generators is with a low-resistance grounding system, where resistance is calculated to allow for relay protection to selectively operate. These current values are often around 400 amps for new systems, but can be as high as 2,000 amps for larger, older systems.
A solidly grounded system will allow for the highest ground faults but will provide the most control of over voltages. A solidly grounded system has the highest probability of escalating into a phase-to-phase or three-phase arcing fault, particularly for 480-volt and 600-volt systems. In addition, severe arc flash and burning can occur from a phase-to-ground fault in a solidly grounded system.
The engineer or system designer should be familiar with all of the common methods of grounding standby generator systems. Certain system parameters and the National Electrical Code will dictate specific grounding practices. In addition, required system uptime and site availability can dictate the use of high or low impedance grounding systems.
Additional NEC grounding provisions
This section of the NEC also indicates that provisions indicated in section 250.36 (A) through (G) shall be met. These provisions are too extensive to be completely detailed in this article, but in summary, they indicate:
- The ground impedance shall be installed between the grounding electrode conductor and the system neutral
- The neutral point of the transformer or generator to the connection point of the grounding impedance shall be fully insulated
- The system neutral conductor shall not be connected to ground except through the grounding impedance
- The conductor connecting the neutral of the transformer or generator to the grounding impedance shall be permitted to be installed in a separate raceway
- The equipment bonding jumper shall be un-spliced and run from the first system disconnecting means to the grounding side of the grounding impedance
- The grounding electrode conductor shall be attached at any point from the grounded side of the grounding impedance to the equipment grounding connection at the service equipment of first disconnect
- The equipment bonding jumper shall be sized based on 250.36 (G)
Consult the National Electrical Code for more information on this subject.
References
- Cummins Onan White Paper on Transfer Switches.
- IEEE std 141 - 1993, Electrical Power Distribution. Chapter 7, Grounding
Articles in This Series
- Part 1: Sizing and Code Issues
- Part 2: The Effects of Harmonics
- Part 3: Complying with the Codes and Controlling Noise
- Part 4: Fuel Configurations for Standby Gensets
- Part 5: Paralleling Generators in Critical Applications
- Part 6: Generator Sizing and UPS
- Part 7: Commissioning, Training and Long-Term O&M Programs
- Part 8: Basic Calculations for Sizing Generators and the Impacts of Certain Loads
- Part 9: Design Criteria for Grounding
- Part 10: Generators and the 2005 NEC