Versatile Track System Boosts Skid-Steer Traction and Flotation
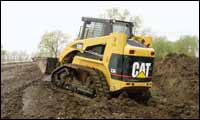
Loegering's Versatile Track System (VTS) increases a skid-steer loader's traction and flotation in soft material. The VTS lengthens the machine's wheelbase, resulting, says Loegering engineer Ron Hansen, in added stability when backing out of a hole with a load, or when driving onto a trailer without a front-mounted attachment.
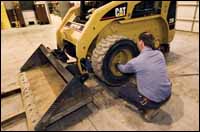
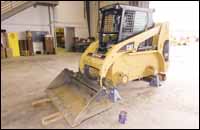
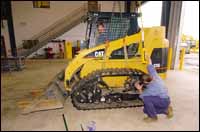
Local 150 instructor/technician Jim Yasko (above) pops the wheels off the Cat 236 skid-steer, which sits ready (center) for a new type of mobility. Local 150's Sean Connelly (right) aligns the VTS sprocket with the 236's rear hub (via an overhead hoist), while Yasko (in cab) carefully powers the drive system to facilitate the process.
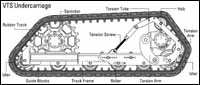
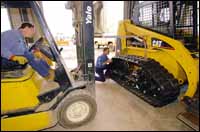
Yasko and Connelly installed the second VTS module with the help of forklifts. Although this method was not quite as handy as using the overhead crane, it proved an effective way to install the VTS.
The Versatile Track System (VTS) manufactured by Loegering is a rubber track undercarriage, complete with suspension, that bolts directly onto a skid steer's standard hubs. By leveraging forward placement of the front idler wheel, it enhances flotation in dirt, sand, and other soft material while boosting overall stability, especially when digging, backing out of trenches, or hauling and dumping heavy loads.
We got the chance to tag along on a recent installation demonstration, and were amazed by the improved functionality and performance of the model selected = a Caterpillar 236 skid-steer loader.
And before we forget to mention: the process went from start to finish in less than an hour!
TIME CHECK: Minutes 0 - 22
Beginning the process on a soggy day at Local 150's Apprenticeship and Skill Improvement facility in Plainfield, Ill., the first thing you notice is the size and weight of the add-on. The VTS package consists of a complete independent crawler-undercarriage assembly for each side of the machine. And at 1,500 lbs per side, the VTS is no lightweight upgrade. Subtract the weight of the wheels, and the net gain in machine weight is still around 2,200 lbs.
The foundation of the VTS is a beefy, adjustable track frame (tunnel) that telescopes at its midpoint to accommodate varying skid-steer wheelbase lengths. This design extends the skid-steer's wheelbase by about 22 inches when comparing the distance between the centerlines of the skid-steer's wheel hubs with the centerline distance between the front and rear idlers of the VTS.
Starting with the Cat 236 on blocks, we removed the machine's wheels and installed the VTS on the left side with the assist of an overhead crane. Basic installation entails indexing the studs in the skid steer's wheel hubs with mounting holes in the VTS sprocket and the flange on the VTS front hub. The front hub can be moved several inches to accommodate alignment. And when secured to the machine, the unit's front wheel hub simply spins the VTS hub and transmits no power to the undercarriage.
TIME CHECK: Minutes 23 - 48
Our guys opted to install the right side with a forklift, because not everyone making the installation will have the luxury of an overhead crane. First, they mounted the front of the undercarriage. Then, with one guy the cab, they started the engine and slowly rotated the wheel hubs to index the sprocket and rear wheel hub. Tightening the mounting nuts to 190 pounds-feet and checking the track tension completed the installation. The right side, with forklift assist, took 26 minutes.
VTS skid steer installation options
It's possible to install an additional up-stop plate on each side to ensure the gussets on the machine's axle hubs don't interfere with suspension components. However, it should be noted that adding these plates will slightly limit suspension travel.
In addition, the Cat 236 has small, bolt-on counterweights at the bottom of the loader towers. The top of the track lugs just cleared the lower front corner of the counterweights. With the increase in operating weight obtained through the VTS, our guys say the counterweights could probably be removed and not missed. But if you make any specialized modifications to your equipment, it's always best to have your dealer or another professional do it for you to preserve any warranties or agreements that cover the machine.
The finished results
VTS installation provided bi-directional suspension that adjusted independently from one side of the rig to the other. The forces that displace the track vertically are transmitted through the torsion arms and into the torsion tube where shock loads are dissipated as the cords compress. The net effect is that the undercarriage is allowed to flex for a better ride.
Plus, the suspension automatically applied the track undercarriages back to the ground. In doing so, the VTS is able to maximize track footprint by evenly distributing horsepower and improving stability on uneven terrain. And by placing the rear idler farther back than the rear hub position, VTS provides substantially more stability when traveling up inclines or negotiating side hills.
The VTS sprocket is 18 percent smaller in diameter than most conventional skid-steer wheels. This reduction slows the machine about 1 mph to compensate for any potential stress resulting from the added weight of the VTS, according to Loegering engineer Ron Hansen. Although the smaller sprocket also increases torque, he says, independent engineering analysis indicates that the added power produces less torsional stress on the axles than would result from installing over-the-tire steel tracks.
Ready to Compare Skid Steer Loaders Price Quotes?