New Excavator Technology Allows for Smarter Construction
Computers installed in today's 30- to 40-ton hydraulic excavators amplify the many aspects of operation by actually making production decisions. Equipment manufacturers have effectively leveraged the cost-effective capabilities of technology to produce excavators that feature:
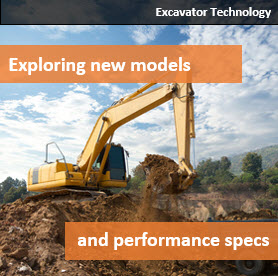
- More powerful engines and hydraulics
- More effective cooling systems
- Longer service intervals
Multiple work modes
The Environmental Protection Agency's 2003 Tier-II emissions deadline brought engine updates across the 30- to 40-ton excavator class. With their electronic fuel-injection controls, virtually all of the engines are more powerful than engines used in preceding models (up to 19 percent more horsepower). And with the ability to fine-tune fuel injection as the work changes, most of the new engines use in the neighborhood of 10 percent less fuel.
Average Excavator Costs
Size range | List price | Hourly cost* |
61,800 to 72,600 lbs. | $256,831 | $78 |
72,601 to 88,000 lbs. | $303,011 | $90 |
* Monthly ownership cost (based on list price) plus operating expenses, divided by 176 hours
Machine controllers now offer operators the choice of multiple work modes, each designed to assign hydraulic priority to the circuits most critical to production in common excavator jobs. For example, stick and boom get flow priority in the digging mode while the attachment circuit gets priority in attachment mode. The problem with previous generations of excavators is that operators had to be trained to use the right mode at the right time. That seldom happened, and productivity and efficiency suffered when work was done in the wrong modes.
To simplify the choices, many of today's machines offer an Automatic mode. The machine's computer senses system pressure and the operator's lever inputs then adjusts hydraulic priorities automatically to accomplish more efficiently what the operator wants to do.
Sensors in the hydraulic systems integrated with controllers on both the hydraulic pumps and engines have made the power-boost feature common. If the machine's working circuits reach standard relief pressure for more than a second or two in tough digging, the systems automatically boost main pressure about 10 percent for a short period (usually around 10 seconds). Machines can handle the heavier load for short spurts, and the extra power can help push through a tough job. Several manufacturers put a button on the joystick that operators can push to boost power on demand.
The availability of work modes varies by manufacturer:
- Caterpillar has eliminated work-mode selections from its 325C L and 330C L
- Komatsu's Galeo system has Active and Economy work modes, a Lifting mode, and a Breaker mode, plus two boom settings - Smooth and Power - that allow operators to customize each work mode
- Hyundai offers a similar control scheme, with Heavy Duty and General settings, as well as a Breaker mode. And the operator can choose High Power or Standard Power in each mode
- Most other manufacturers have limited the choices to Automatic mode and one or two other choices (often just Digging and Attachment modes)
Electronic controls
When you ask manufacturers' excavator product managers which single technology had the greatest impact on their product category over the past 24 months, virtually all of them talk about electronic controls that now do more than just sense conditions. They provide feedback - either at the monitor or in the form of adjustments to hydraulic and engine performance.
It's a sophistication bordering on artificial intelligence that makes the machines more effective and efficient. Electronic systems provide information that improves diagnostic ability and helps owners make the best choices about how to use the machine effectively.
Tracking performance data
Along with the other electronic improvements, many excavators now include built-in data tracking that records all operating parameters, including:
- Engine speed
- Coolant temperature
- Hydraulic pressure and temperature
- Travel time
- Swing time
- Idle time
- Fault codes
- Alarms
To simplify management, data can be downloaded easily with a hand-held computer. Once it's uploaded to a personal computer, it can be graphed for easy analysis and used to fine-tune both the machine and the operator as well.
Simplifying maintenance and extending service intervals
In addition to on-the-job performance, technology is improving durability and ease of service too. For example, today's engines in the 30- to 40-ton excavator class have more heat to dissipate because of intercoolers between turbocharger and cylinder head, so many machines are now cooled by a fan with hydrostatic drive. Responding to information from a thermostat, the engine controller tells the hydrostatic fan drive when to come on and how fast to run. The fan uses only enough power to hold the engine in a safe operating-temperature range. Deere and some others have added an airfoil fan to variable fan drive to save significant horsepower.
It's not a coincidence that there's a service-interval race going on in hydraulic excavators at the same time so much electronic technology is being applied to the machines. Most of the diesel engines in today's excavators are designed for 500-hour oil-change intervals. The engines are working harder than ever. But computer controls have softened the sharp peaks in horsepower demand and they monitor and respond to coolant and oil temperatures and pressures better. New filter technologies are buying time for oil, too.
In the interest of aligning basic service at the same interval as the engine-oil change, manufacturers are applying special metallurgy and seals to bushings and pins in boom, stick and bucket joints to stretch greasing intervals. John Deere and Komatsu excavators are at 500 hours, and all the front-linkage pins except for the bucket joints on Cat and Case machines now require grease only at 1,000-hour intervals.
High-end hydraulic filtration and more-effective cooling have extended hydraulic-oil service intervals as long as 4,000 hours. For example, Link-Belt's LX Series machines come standard with a factory-installed bypass filtration system called Nephron.
Excavator Specs: 30- to 40-Ton Base Models
Model | Operating Weight (lbs.) | Horsepower | Max. Dig Depth | Lift Cap. (lbs.)* | Arm Digging Force (lbs.) |
John Deere 270C LC | 62,674 | 177 | 23′ 10″ | 20,643 | 26,067 |
Komatsu PC270LC-7 | 62,830 | 179 | 21′ 2″ | 22,000 | 33,290 |
Hitachi Zaxis 270LC | 62,870 | 173 | 23′ 9″ | 20,700 | 26,000 |
Liebherr R934B | 62,920 | 194 | 23′ 5″ | 19,750 | 27,500 |
Caterpillar 325C L | 63,100 | 188 | 23′ 3″ | 21,150 | 26,200 |
Volvo EC290B LC | 64,230 | 192 | 24′ 0″ | 24,270 | 30,340 |
Link-Belt 290LX | 64,400 | 177 | 23′ 5″ | 21,910 | 25,850 |
Case CX290 | 64,725 | 182 | 23′ 5″ | 21,916 | 28,101 |
Daewoo Solar 300LC-V | 65,270 | 197 | 24′ 1″ | 22,200 | 29,500 |
Hyundai R290LC-7 | 66,270 | 183 | 24′ 7″ | 21,050 | 30,310 |
Hyundai R320LC-7 | 71,000 | 259 | 23′ 4″ | 24,820 | 32,470 |
Komatsu PC308USLC-3 | 72,066 | 179 | 21′ 0″ | 23,400 | 30,640 |
JCB JS330 | 72,098 | 219 | 24′ 3″ | 22,248 | 29,547 |
John Deere 330C LC | 72,492 | 246 | 23′ 11″ | 26,089 | 37,396 |
Hitachi Zaxis 330LC | 73,500 | 247 | 24′ 3″ | 25,800 | 37,000 |
Komatsu PC300LC-7 | 73,629 | 242 | 24′ 3″ | 26,400 | 37,040 |
Volvo EC330B LC | 73,740 | 247 | 24′ 2″ | 29,620 | 38,810 |
Daewoo Solar 340LC-V | 74,700 | 247 | 25′ 2″ | 26,310 | 38,400 |
Liebherr R944B | 77,000 | 241 | 24′ 5″ | 26,500 | 31,680 |
Caterpillar 330C L | 77,113 | 247 | 24′ 3″ | 26,950 | 36,300 |
Link-Belt 330LX | 78,000 | 247 | 24′ 1″ | 28,890 | 36,850 |
Case CX330 | 78,043 | 259 | 24′ 1″ | 28,925 | 36,846 |
Hyundai R360LC-7 | 79,590 | 280 | 24′ 7″ | 28,510 | 37,280 |
Source: EquipmentWatch.com
* Over the end, at 20-foot radius, at ground level
Ready to Compare Excavators Price Quotes?