Extend the Life of Your Caterpillar Bulldozer
Doze Front to Back
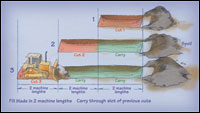
The most effective way to bulldoze volumes of dirt is to start two tractor lengths from the end of the intended cut. Fill the blade as quickly as possible in first gear - usually within two tractor lengths - and start a spoil pile. On the second pass, back up two tractor lengths further than the start of the first pass, fill the blade again, then carry the load through the slot created in the first pass. Repeat the process, carrying the load further with each pass, until the slot stretches the length of the intended cut. The walls of the slot can extend the tractor's blade load by as much as 30 percent.
Start at the Spoil
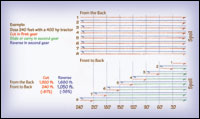
Front-to-back slot dozing cuts undercarriage costs as it improves productivity. Driving in reverse causes the worst track wear. Working front to back, you only have to reverse the tractor the distance of the previous push plus two tractor lengths. Compared to backing up the entire length of the cut, this reduces reverse operation - by 38 percent in the example of a 240-foot cut. It reduces operating costs, and increases dirt-pushing time.
Steep hourly cost makes operating efficiently more important to crawler dozers than most other construction equipment. The cost is largely associated with undercarriage wear, so the best dozer operators make every move count whether they're doing production earth moving, finishing, or clearing land.
Common production dozing mistakes
Some of the best ideas for improving dozer productivity defy operators' assumptions.
"A lot of operators who are doing production dozing think they should make long cuts. They want to see dirt boil or roll in front of the blade," says Brad Van De Veer, senior product consultant at Caterpillar's Edwards Demonstration/Application Center. "In reality, the blade will only hold so much dirt. Once it's full, you start losing dirt off both sides of the blade, leaving windrows that will have to be moved again. It wastes horsepower and fuel, and it can cause track slip and undercarriage wear.
"You should be able to get a full load on the blade in two lengths of the tractor at the most - and that applies to any size tractor. Once the blade is full, you stop cutting and slide the dirt in front of the blade."
Short, aggressive cuts set up what is perhaps the most energy-saving way to doze dirt - what Caterpillar calls "front-to-back or slot dozing."
"You start one to two tractor lengths back from where you're going to move the dirt, instead of on the opposite side of the field," says Van De Veer. "Fill the blade and start a pile or fill the area."
Bulldozing mistakes that can cut down on operating efficiency include:
- Not allowing enough berth between the bulldozer and rocks, logs, debris, and ditches.
- Spinning the track; this can create ruts in material.
- Starting in a high gear when feeding the blade into the ground.
- Partially loading the blade, making it more difficult to control.
Put it into action: Best bulldozing practices
The next step is to back up one to two tractor lengths behind the start of the first cut, fill the blade, and slide the load, or carry it, through the slot created by the first pass and deposit it on the spoil pile. Use first gear to aggressively fill the blade. In small and medium sized tractors, shift up to second when sliding the load. Repeat the process, sliding a full blade load through the slot further with each pass.
Working in the slot increases blade load by as much as 30% and prevents material from falling from the blade.
Front-to-back dozing cuts undercarriage costs. Instead of backing the entire length of the cut after each push, you only reverse the tractor the distance of the previous push plus one or two tractor lengths.
"Running in reverse causes the most undercarriage wear, and it's the most unproductive time in the work cycle," says Van De Veer. "Working front to back, you reduce the amount of reverse operation, which decreases operating costs and increases productivity."
Van De Veer says slots can be dug as deep as the blade is high.
After the first slot is completed, back up to about two tractor lengths from the spoil and move over, leaving about one-third of a blade width between the edge of the blade and the first slot. This berm will hold material in front of the blade on the second slot.
After the slots are cut to the desired grade, the work pattern reverses for clearing the berms.
"You want to work from the rear of the cut, or the opposite end from the spoil, rather than front to back," says Van De Veer. "Load up the blade quickly, and use blade tilt to steer into one of the slots to carry the load to the pile or fill."
A crisscross pattern will help keep the cut level: If you slide the load up the left slot on the first pass, swing into the right slot on the second pass, and then back to the left slot on the third.
Helpful guidance for fine grading and finishing
Some simple techniques will make fine grading more efficient, too.
A videotape called Tips From the Pros: Crawler Dozer from VISTA Start Smart Training recommends: "When finishing or dressing, working with a partially loaded blade is better than working with an empty one. It smooths out the ride and distributes fines across the blade.
Load only half of the blade to keep windrows on one side of the machine. The blade can overlap previous passes to act as a depth guide.
"The smoothest finishing jobs happen when dirt is worked from at least two different directions [passes oriented at 45- to 90-degree angles to each other]," according to VISTA. "It's the same principle as an orbital sander on wood. Irregularities get smoothed out if attacked from more than one direction."
Mindful operation improves fuel economy
Heavy machinery manufacturer Komatsu confirms that bulldozer productivity and fuel consumption depend directly on the geography of a jobsite, such as whether the ground is level or sloping. Soil composition can also impact both factors.
While it may be difficult to cut down on fuel waste during operation since a bulldozer dozes at full power using its own weight as leverage, efficient operating protocol and fuel monitoring while idling can help keep fuel costs to a minimum.
Komatsu recommends practicing idle stops to avoid times of high idling. As an example, when a bulldozer is waiting for a dump truck, fuel costs can be reduced by eliminating high idling; low idling or deceleration can help to slow engine speed and reduce fuel consumption. Komatsu confirms that turning off the engine for just an hour per day could provide an annual savings of 642 gallons.
Ready to Compare Bulldozers - INACTIVE Price Quotes?