Backhoe Loader Basics
The backhoe loader is one of the most common pieces of heavy equipment on job sites large and small. The combination of two useful tools into one machine make the backhoe loader a must-have on all kinds of construction and repair work.
The standard backhoe is a diesel-powered, four-wheeled vehicle with the operator's cab in the middle and tools on each end. On the front, it has a loader: a wide bucket on dual arms that's used to either pick up loose piles of material or push dirt back into a hole when a job is finished. The rear end has a backhoe - a hydraulic-powered digging scoop on a three-jointed arm - designed to dig through hard earth. The operator needs only to turn around in his seat to switch from digging a hole to filling it back in again.
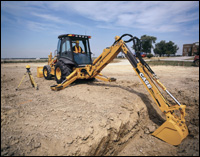
Frequently used on construction sites, the Tier 4 interim compliant engines combine with features geared toward efficiency and productivity in an industrial setting. Most common are models that range in horsepower from 97 to 110 HP and include automatic ride control system, fast backhoe boom positioning and transmissions that produce excellent force and capacity while minimizing fuel consumption.
Operating features to look for
Whether your intended application is construction, agriculture, or some other type of earth-moving scenario, the first consideration in choosing a backhoe loader is digging depth:
- Full-sized backhoes usually reach down to between 14 and 16 feet
- Compact backhoes can typically dig around 8 to 10 feet
The inverse can also be important. If you need to load dump trucks of a certain size, make sure the loader has an appropriate "dump height" to do the job.
On crowded job sites, four wheel steering offers greatly improved maneuverability. And in the tightest spots, "crab steering" lets you turn the front and rear wheels independently. Four wheel steering is fairly uncommon but rapidly gaining popularity. More common is four-wheel drive, which is hard to beat for traction on muddy or loose ground. A 4 x 4 x 4 backhoe has four-wheel drive and four-wheel steering.
Attachments provide flexibility
While the digging scoop and the loader bucket are by far the most popular tools used on backhoe loaders, there's been a trend in the industry in recent years towards using additional attachments to increase the machines' flexibility. For example, switching from the bucket to forks lets you use your backhoe loader to easily move pallets around without the expense and hassle of bringing a forklift to the job site.
This functionality is one of the primary reasons backhoe loaders continue to be popular for agricultural applications. The wide range of buckets and attachments maximize the investment by enabling the machine to perform most if not all of the tasks on a large farm.
If you want to be able to use multiple attachments, look for a backhoe that includes a quick coupler. A quick coupler is an industry-standard connection for various types of construction equipment, and includes connections to the loader's hydraulic system for powered attachments.
There are many different types of attachments that can be used on a backhoe loader. The front of a backhoe loader can be outfitted with forks, grapples, and powered brooms. The back can use hammers, thumbs, and grinders. Either end can be fitted with multipurpose buckets of varying widths for lifting, carrying, and dumping different types of materials.
Backhoe loader pricing
Major pieces of construction equipment like backhoe loaders don't come cheap. But before you develop a case of sticker shock, consider that you'll be using your new backhoe loader for 10 years or more, and the upfront cost won't seem quite as high.
- New prices: Average costs for a 14' to 15' backhoe are around $70,000. 15' to 16' models go for around $84,000, and those over 16' can be $110,000 or more.
Due to these steep prices, you may want to investigate used backhoe loaders. Prices drop considerably once the machines have a few thousand hours of use on them, with 2,000 to 3,000 hours being a common range for used backhoes. That said, if you're willing to pay a little more but still want to get under MSRP on the new model, many used backhoes are available with as little as 60 hours on them.
And don't forget to factor in the year it was manufactured - you'll need to be careful about maintenance costs. A few dings and some peeling paint might not matter to you, but a failing transmission certainly will, and could be costly to replace if it's more than 20 years old. Take extra care to ensure that you're buying from a reputable dealer when buying used backhoes.
- Used prices: Used backhoe loaders cost between $25,000 and $42,000 for smaller models and are available through reputable dealers as well as private owners. Larger models will be in the $50,000 to $70,000 range.
Additional backhoe loader considerations
- Regulations require tier-II engines on all new backhoes, mainly because they produce fewer emissions than older diesels. However, improvements to the technology give tier-II engines more torque and horsepower with better fuel economy.
- Older backhoe loaders use hand and foot levers to control the various functions - newer backhoes feature much easier-to-use "pilot controls:" dual joysticks that provide full control with less stress on the operator.
- Cabs are becoming more like automobile interiors: they're larger, provide better sight lines, and can include extras like suspension seats, climate control, and 12-volt outlets for cell phones or other accessories. These aren't just frills: keeping the operator comfortable increases productivity.
- Lifting capacity varies from one end to the other: one loader might be able to lift 16,000 lbs with the loader, but only 2,500 lbs with the backhoe.
- Backhoes have two stabilizer legs located right behind the rear wheels. These legs support most of the weight when digging, reducing stress on the wheels and providing a steady digging platform. The stabilizer on the backhoe loader you choose should have both grouser shoes that provide a firm grip on dirt, and rubber-padded shoes for use on asphalt.
- In environments that are particularly tough on air-filled tires - demolition sites and recycling operations, for example - foam-filled rubber tires are a good option. They're more expensive, but will save you the expense and down time of blowouts.