Spray Paint Booth Basics
Used for a variety of industrial applications, from metal and woodworking to painting cars, trucks and other vehicles, the modern spray paint booth delivers a cleaner, safer and functionally optimized workspace. Containing hazardous elements, from dust to paint, an enclosed booth preserves the health of your employees and the surrounding environment while controlling over spray and significantly reducing costly prep time.
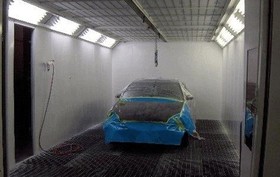
In addition to keeping harmful pollutants in, a spray paint booth also blocks external elements from contaminating your project. The painting area is often enclosed to prevent dust and other contaminants from coming into contact with the objects being painted. Contaminants lessen the quality of a paint job and further add to operating costs.
Paint booths intended for industrial use can be extremely large, such as those built to accommodate trucks or aircraft. But there are also models small enough for handheld objects. Whether you're painting porcelain, furniture or an airbus, the setup is basically the same. Here's how it works.
How Does a Spray Paint Booth Work?
Before spray painting anything, workers need to completely clean the objects to create a smoother surface for painting. The painter then makes sure that the airflow and air-pressure mechanisms are working properly. Using a variety of filtration media that includes filter pads, water, and moving air, a spray paint booth is designed with an internal airstream that gathers the solids, known as particulate emissions, and directs them to the filtration medium.
Balanced airflow and pressurized air are key to quality painting. As a result, new air make-up (AMU) systems have air-pressure sensors that automatically control the amount of air you need via fans, filters, and compression.
Another new technology in air control is recycling. Through this method, the air recycles and completely exhausts itself of solvents in the burner before entering the painting booth, maintaining higher temperatures and fresher air. This results in quicker drying, harder finishes, and lower energy costs.
As the process begins, a professional painter or robotic system uses a spray gun or similar device to apply the coating material. The power and direction of the air, the effectiveness of the filtration, and the type of coating equipment used (wet paint versus powder coating) determine the overall efficiency of the coating operation, as well as the quality, durability, and gloss of the finish.
Some of the primary components in the process include:
Cabin or booth construction. Booths may be closed-faced (with four walls and a ceiling) or open-faced (with three walls and a ceiling). The walls must be made of non-combustible material like thick metal, concrete, or masonry. They must be finished with pre-coated steel, wet-painted finish, or a powder coating to maintain smoothness. The floor must likewise be constructed with watertight concrete or other fire-resistant material.
Exhaust fans. Exhaust fans balance airflow and air pressure, and prevent paint contamination. They may either be down-, cross-, or side-draft. In a down-draft exhaust fan, air enters the booth from the ceiling, while in a cross-draft and a side-draft, air enters from the sides.
Exhaust filters. Paint booth exhaust filters are designed to eliminate dust and other airborne particulates to create a clean and healthy painting environment. They should be durable, have long life spans, and capture particulates efficiently.
Duct-work. Whether you're exhausting through the wall or the roof, any 45- and 90-degree turns must be configured with the exhaust-fan system to reduce the recirculation of fumes to protect workers and products.
Electrical components. Electrical switches must be installed in non-hazardous locations. Lighting must be enclosed by wired glass with a secure vapor seal.
Ready to Compare Spray Paint Booths - INACTIVE Price Quotes?